Renewable Natural Gas (RNG) plants play a vital role in converting food and other organic wastes into clean energy through anaerobic digestion. While plant operators are familiar with the dangers of poorly ventilated spaces and hydrogen sulfide (H2S) accumulation, this article sheds light on three common scenarios where H2S can pose a threat in well-ventilated spaces and at well-maintained digester sites. Understanding these risks can improve the safety and efficiency of RNG plants. Let’s explore these risks and possible remedies to prevent a potential disaster.
1. Rapid Release of Dissolved H2S Gas: Under normal circumstances, feedstocks being received at an anaerobic digester may contain H2S dissolved in alkaline or neutral pH feedstocks. When these H2S-rich feedstocks are mixed with a low pH counterpart the H2S becomes less soluble and is quickly converted to a gas. For example, mixing acidified industrial fats, oils, and grease (FOG) waste and H2S-rich alkaline manure or brewery waste could release a surge of H2S bubbles from the feedstock storage tank. Such instances can endanger plant workers by exposing them to a cloud of poisonous gas.
2. Sulfuric Acid Formation and Corrosion: In some digesters, air injection is used to lower the H2S concentration present in the biogas. While this method economically mitigates H2S in the biogas, it introduces a new concern. Sulfur-oxidizing bacteria use the oxygen in the air to convert part of the H2S gas to sulfuric acid. This sulfuric acid can then corrode concrete digester walls, roof structures, or other unprotected materials in the digester’s headspace. If left unchecked, corrosion can cause significant damage to plant infrastructure, leading to costly repairs and potentially hazardous conditions for workers if structural digester elements collapse.
3. H2S Accumulation in Anaerobic Sediments: Digestate storage lagoons, common to many RNG plants, usually accumulate anaerobic sediments over time. These sediments can serve as reservoirs where biogas containing H2S can build up unnoticed. Disturbing the sediments before field application or during routine mixing can cause the rapid release of trapped H2S gas, posing a risk of poisoning plant personnel.
Preventive Measures
To mitigate these unexpected risks, plant operators should be vigilant and take appropriate preventive measures. Here are four practical solutions:
1. Feedstock Management: Characterizing feedstocks to identify the potential for hydrogen sulfide generation and release can help operators proactively identify potentially dangerous situations. Once operators know the risks, they can follow simple rules to manage feedstock mixing to avoid a sudden release of H2S. Maintaining separate storage and mixing facilities for feedstocks with significantly different pH levels or sulfur concentrations can prevent dangerous interactions while giving greater control to optimize digester performance.
2. Sulfide Treatment Systems: Sulfide treatment systems can be economical and effective when designed to meet the needs of the plant. Factors that should be considered include:
- feedstock sulfur concentration,
- digester biology’s sensitivity to sulfide toxicity, and
- offtake or engine requirements.
For large-scale systems where biogas is being converted to RNG, large capital, low consumable treatment technologies are often considered during the initial process design stage. For smaller systems and existing digesters, in-situ iron addition can achieve H2S reduction targets. It is important to be aware that the chemical availability of iron additives can vary substantially between additive type and manufacturers.
Air injection for in-situ biological sulfide removal has very low costs per pound of sulfide removed. If a digester has been designed with a high-surface-area headspace and has regular dome maintenance, air-injection may be a promising avenue for sulfide removal. If the digester has not been designed to accommodate sulfur oxidizing bacteria, other options may need to be explored. Adding iron supplements to a digester can quickly reduce hydrogen sulfide concentrations in biogas and improve digester health. If lower H2S concentrations in biogas or RNG are required, adsorbent media beds and scrubbers should be considered. Figure 1 illustrates some available options and general guidelines for when the different technologies might be selected. While the figure is a useful guide, it is important to consider the specific needs of your project to minimize the overall risk and cost.
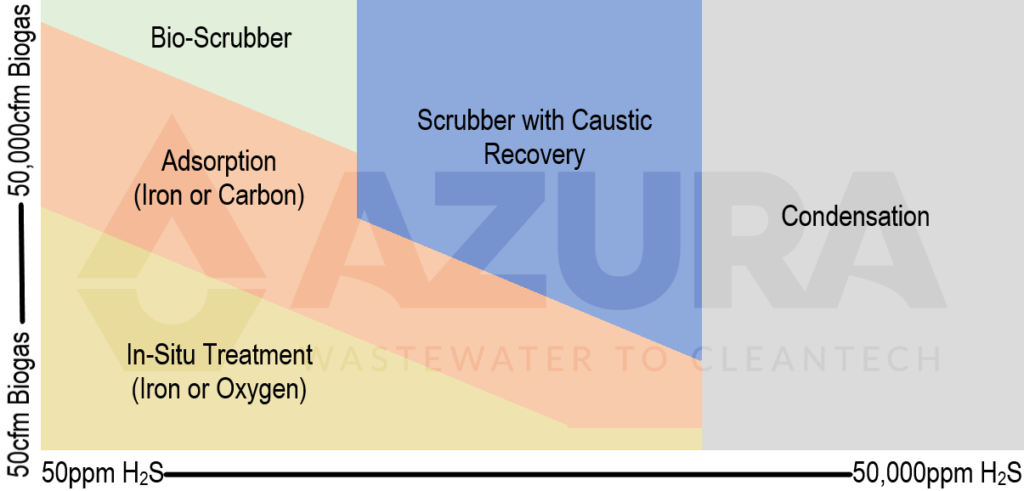
3. Digestate Management: Digestate storage and disposal or land application can be managed to minimize odor, tank clean out costs, and avoid dangerous H2S release. Owners and operators can benefit from understanding the solids and sulfur loadings in their digestate to manage the risks with minimal cost. For example, high solids digestate storage tanks and lagoons should be mixed to prevent the accumulation of large H2S bubbles in the sediment, as well as reducing the frequency of lagoon clean outs. In-situ treatment systems, including iron-based additives and oxygen injection, can reduce the load of sulfur in the digestate that can be converted to H2S gas. Reducing sulfide concentrations in digestate reduces odorous emissions and risk to operators.
4. Monitoring and Safety Protocols: Online monitoring of H2S in biogas and in enclosed spaces is standard practice for RNG plants. However, the safety protocols and gas treatment systems to respond to high H2S concentrations are not standard and should be considered to protect workers, to protect equipment, and to maintain the gas quality requirements for offtake. If an increase in H2S concentration is detected, iron-based additives can be added to the digester to remove H2S from solution. Additionally, regular inspection and maintenance of the flare and biogas handling system can identify corrosion early.
Conclusion
Hydrogen sulfide is a well-known risk to human health, equipment, and profitability. While the acute risks of working in confined spaces and corrosion in engines are often discussed, the risks associated with mixing feedstocks, corrosion of digester structures, and lagoon sediments are often overlooked. Understanding these risks not only helps to avoid injuries, but also provides insight into the many biochemical processes at work in an anaerobic digester. By considering each stage in the plant from receiving, to gas production, to digestate storage, and developing safety protocols accordingly, a robust risk management strategy can be developed. Developing a strategy that considers the many biochemical processes present in an anaerobic digester can improve both plant performance and safety. By embracing preventive strategies and scientific insights, we can safeguard personnel, protect property, and ensure the continued success of renewable natural gas projects, leading the industry towards a cleaner and safer energy landscape.
Authors
David Ellis, Principal Engineer
Peter Quosai, Bioprocess Analyst
*This article was first published in Issue 4 of Biomass Magazine.
Related Articles
Watch Your Step! Slips, Trips, and Falls in An Anaerobic Digester Facility
Slips, Trips, and Falls are common workplace accidents and biogas and RNG plants are no exception. This article highlights risks unique to these plants and proactive measures to keep your anaerobic digester facility running safely. Read the full article.
Effectively Ensuring Safety in Biogas Facilities
This article covers five key categories of safety hazards and four hazard control methods within a biogas facility to better protect employees, the surrounding community, and our environment. Read the full article.
Get Insights from the Bioprocess Experts Right to Your inbox
Sign up to the Discover Digesters Newsletter to access Azura’s best practices, field-tested advice, and insights into the anaerobic digestion & industrial wastewater treatment industries.
By submitting this form, you are consenting to receive marketing emails from: Azura Associates. You can revoke your consent to receive emails at any time by using the SafeUnsubscribe® link, found at the bottom of every email. Emails are serviced by Constant Contact.