Anaerobic digestion is an established method for managing organic waste, creating renewable energy, and also producing valuable soil amendments. Prioritizing safety at biogas and renewable natural gas (RNG) facilities helps maintain smooth operations. From toxic gases and biohazards to common industrial safety risks, there are many aspects to consider in maintaining a safe working environment. This article covers five key categories of safety hazards and four hazard control methods within a biogas facility to better protect employees, the surrounding community, and our environment.
These hazards apply to most biogas and RNG facilities, though if you are at a facility that processes food waste, municipal source separated organics (SSO), or the organic fraction of municipal solid waste (OFMSW), there may additional hazards associated with you specific type of facility.
Understanding the Hazards
The presence of hazardous gases may be the best-known concern for operational health and safety in a biogas facility. While hazardous gases should be treated seriously, they are not the only safety hazard to consider. Safety protocols at a biogas facility should address:
- Hazardous Gases
- Biohazards
- Fire and Explosion Risks
- Maintenance and Repair Procedures
- Common Industrial Risks
1. Potential Hazard – Hazardous Gases
Gases like ammonia, methane, carbon dioxide, carbon monoxide, hydrogen sulfide (H2S), and volatile organic compounds (VOCs) pose health risks ranging from irritation to death. Methane and H2S have the greatest potential impact on health and safety. Methane is highly flammable and explosive, while H2S can be extremely toxic even in small amounts. These hazardous gas risks are not unique to biogas and RNG production facilities. Trained sewage treatment plant operators should be familiar with these gases and able to manage the risks appropriately.
A particular risk at organic waste processing sites comes from mixing different food waste and other organic waste materials in raw feedstock holding tanks. Sometimes, the waste can be septic and contain significant H2S and dissolved sulfides. If an acid waste is then mixed in with this tank, the resulting chemical shift can result in rapid H2S formation in the feedstock holding tank. This H2S can be released from the liquid and potentially result in a serious, or even deadly, situation for operators in the area.
- Potential Hazard – Biohazards
Biogas facilities often deal with a wide range of organic materials, including liquid and solid food wastes, manure, and sewage sludge. Organic waste often contains biohazardous materials and that risk cannot be eliminated because biogas cannot be produced without it. We need to understand and manage these risks safely.
Organic waste often contains a variety of microorganisms including bacteria, viruses, molds, and parasites that can cause infections and diseases. Sewage biosolids host a plethora of pathogens. At food waste digesters or any biogas facility treating chicken or other raw meat, operators are at a risk for exposure to salmonella and E. coli. SSO or OFMSW digesters may see materials like pet waste, diapers, and hygiene products in the feedstocks.
The risk of exposure to biohazards is highest where an operator handles the feedstock or digestate. Areas like the feedstock receiving pits and digestate holding tanks are common points of exposure. During planned maintenance, operators also face increased risks when cleaning or maintaining these tanks and any piping, pumps, valves, instruments, or other equipment that touches the waste. Flushing and sanitizing systems before planned maintenance is routine. But what about during a breakdown?
Imagine a cracked pipe spraying raw feed material and aerosolizing the material and putting all that ick into the air! The same risk can also occur when operators use hoses to spray off equipment or wash down the feedstock area.
Including air quality controls in the design of the ventilation system, hygiene protocols, adopting industry best practices, and the appropriate use of personal protective equipment (PPE) can all work together to reduce the risk for those exposed to these biohazards.
- Potential Hazard – Fire and Explosions
Beyond the flammability of biogas, the accumulation of dust around digestate drying operations also aggravates the risk of fire and explosions in biogas facilities. The dust particles can be stirred up by vehicle traffic and moving equipment. Dust explosions are a great risk as a secondary event—if a truck accidently hits part of the building, accumulated dust on the tops of piping, ductwork, and structural steel can be disturbed, becoming airborne. This airborne dust is then the highest risk of a dust explosion if there is an ignition source nearby. Potential ignition sources include:
- Friction from mechanical parts such as hot bearings,
- High-temperature equipment such as heaters, but also forklift exhaust piping,
- Electrical sparks, including static electricity as well as from motors and lighting,
- Common electronics and hand tools such as flashlights and power drills, and
- Flames from activities like smoking, welding, or other hot work.
Increased dust levels not only raise explosion risks but also deteriorate air quality for on-site operators and the surrounding community.
- Potential Hazard – Increased Exposure to Hazards During Maintenance
Planned maintenance and repair activities can lead to exposure to biohazards, chemical hazards, and the accidental creation of confined spaces—all of which increase safety risks for workers. Some of the common, repair events involving increased safety hazards are gas leaks, foaming due to digester upsets, and spills. Similarly, a planned maintenance event like digester biological startup or re-seeding can result in creating temporary conditions that need special attention.
For example, after digester repairs and reseeding, the digester headspace may need to be purged of oxygen to prevent creating an explosive air and methane mixture as the process biology begins creating methane.
It is important to take safety precautions even during routine maintenance and operations. Routine and repetitive tasks can pose a physical health risk to operators through overuse injuries. Repetitive tasks can also reduce an operator’s focus which can lead to accidents. Personal factors including tiredness can further retract an operator’s focus away from the task. Managers can reduce this risk by implementing job rotations, adequate break times, and automation.
- Potential Hazard – Common Industrial Site Safety Hazards
Biogas facilities have all the same hazards that are common across most industrial sites. These hazards include:
- slips, trips, and falls;
- vehicle and heavy equipment traffic; and
- mechanical equipment hazards.
While these are common safety concerns it is important to consider how they apply specifically to anaerobic digestion facilities.
- Organic wastes often contain Fats, Oils, and Greases (FOGs). This FOG material poses a heightened slip, trip, and fall risk if there is a spill or even a small amount of material on the ground, like when a hose has been disconnected. The area can look simply wet, but in fact be greasy and very slippery. These FOG areas are also particularly challenging to clean with a simple cold-water hose.
- Increased vehicle traffic for moving feedstock and digestate on and off-site can lead to congestion. Congestion can be aggravated during poor weather when trucks may arrive close together in time resulting in increased risk of accidents and injury. During poor weather, visibility in the yard area can also be reduced because of rain or snow. Site layout planning can mitigate this risk as can enhanced operator procedures around yard operations during low visibility periods.
- Rotating equipment engineering to cut, shred, and break down coarse food waste materials in a biogas facility present a particular risk to operators. The need for extra attention to be paid to placing and maintaining equipment guarding cannot be over stressed.
Hazard Control Methods
Hazard control methods can be divided into four types. These include:
- Elimination and Substitution
- Engineering Controls
- Administrative and Work Practice Controls
- Personal Protective Equipment (PPE).
Each method plays a distinct role in minimizing risks and enhancing safety within a biogas or RNG facility.
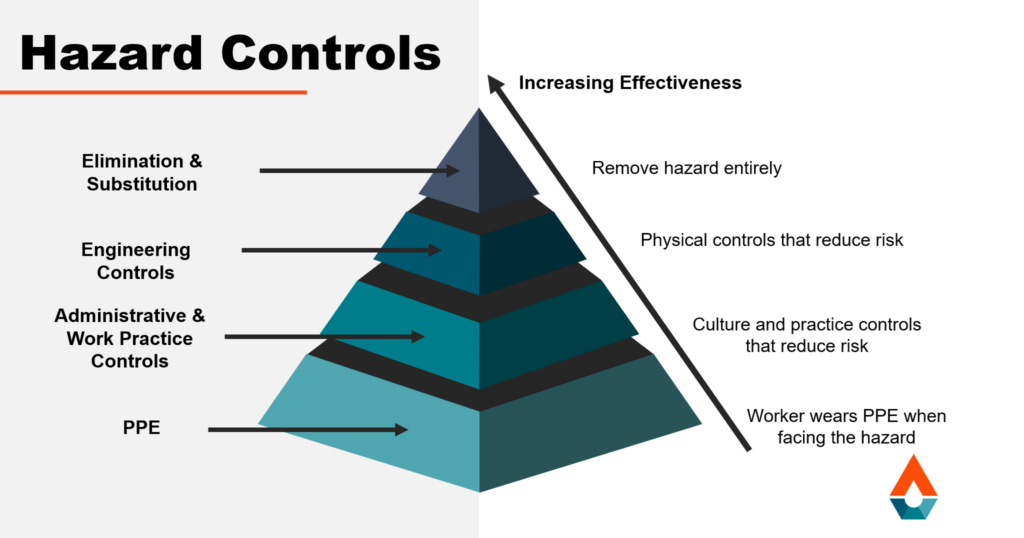
- Elimination and Substitution:
- Elimination: This hazard control method involves completely removing the hazard. In biogas facilities, various components like mixers, engines, storage tanks, and other processing units often require regular maintenance and inspections; sometimes even performed at heights. To eliminate the hazard of working at heights, technologies can be chosen where maintenance points are located at ground level. For example, using mixers that operate from the bottom of digesters instead of the top removes the need for personnel to access elevated areas. This change eliminates the risk of falls and injuries associated with working at heights to access that piece of equipment.
- Substitution: Substitution involves replacing the hazard source with something less hazardous. For example, some biogas facilities use acidic liquid ferric chloride to reduce hydrogen sulfide (H2S) gas production in the digester and digestate. However, by substituting liquid ferric chloride with powdered forms of iron (i.e. iron oxide or iron hydroxide), the risk of spills and leaks of this corrosive chemical is significantly reduced. Powdered iron additives are easier to handle, clean up, and eliminate the potential for splashing, making it a safer alternative for operators. Additionally, using an automated feeder for powdered iron additives further minimizes human contact with the chemical, enhancing safety measures within the facility, specifically reducing the risk of dust exposure from the iron powders.
- Engineering Controls:
- Engineering controls are physical measures that separate the worker from the hazard.
- Design Modifications: The most effective time to reduce risk is during the design and construction phases. Designing processes focused on hazard prevention, such as defining clearances around maintenance points for operators to work, removes significant risk.
- Choosing Equipment with Installed Controls: Equipment with built-in safety measures such as automated systems used for chemical dosing or process monitoring, reduces the time the operators interact with hazardous chemicals and equipment.
- Administrative and Work Practice Controls:
- Training and Certification: Providing comprehensive training and certification programs can give employees a baseline understanding of safety protocols and procedures.
- Emergency Response Plans: Developing and practicing emergency response plans prepares teams to handle unexpected incidents effectively.
- Entry or Work Permit Systems: Implementing strict permit systems for confined space entry restricts tasks within the confined space to the trained and authorized personnel. An entry permit system also outlines the necessary safety precautions to perform those tasks. Similarly, working with ignition sources near flammable materials, also called ‘hot work’, should follow a work permit system.
- Reporting and Documentation: Maintaining detailed records of safety inspections, near-misses, incidents, and corrective actions helps to continuously improve safety practices.
- Personal Protective Equipment (PPE):
- Personal protective equipment is worn by workers to limit exposure to hazards. Note that PPE does not eliminate the hazard and does not guarantee total or permanent protection! For those reasons, PPE is considered the last level and least desirable method of protection when all other methods are not available or not possible.
- Respiratory Protection: Using respirators with appropriate filters protects workers from inhaling hazardous gases or airborne particles.
- Protective Clothing: Wearing flame-resistant clothing, gloves, and eye protection will shield workers from chemical splashes, spills, fires, and other physical hazards.
- Fall Protection: Using harnesses, safety nets, and guardrails prevents falls from elevated areas during maintenance or inspections.
By combining these hazard control strategies and tailoring them to the unique risks of each facility and the specific equipment, materials, and operations there, owners can build a comprehensive safety framework that prioritizes the health and well-being of their employees.
When to Apply Safety Controls
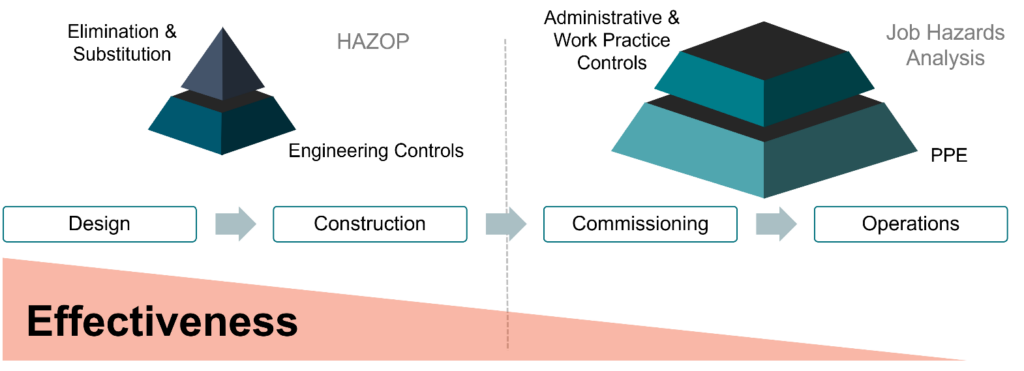
Hazard controls are most effective in early integration during the design and construction phases. Utilizing tools such as HAZOP (Hazard and Operability) studies during design can pinpoint potential risks before they materialize. Additionally, changes to the facility’s equipment, layout, and construction to improve safety are cheaper to implement in these early stages.
As the facility becomes operational, safety considerations shift towards administrative controls and PPE due to the increased cost associated with elimination and substitution as well as engineering control methods. Administrative controls and PPE require site managers and operators to take more personal responsibility for maintaining a safe environment. These extra responsibilities can require plant mangers to chose between hiring more staff to maintain safe operations or to pay for costly retrofits to add engineering controls after the plant is operating. For these reasons, administrative controls and PPE work best to protect workers and the business after hazards have been reduced in the design phase.
Conclusion
Safety is paramount for all biogas facilities. A comprehensive safety strategy begins during the design phase and is then reinforced throughout construction and operations. By understanding the risks, implementing appropriate control measures, and prioritizing safety at every stage, biogas facilities can operate efficiently while safeguarding the well-being of all involved.
*This article was first published in the June 2024 edition of Environmental Science and Engineering Magazine.
Related Articles
Watch Your Step! Slips, Trips, and Falls in An Anaerobic Digester Facility
Slips, Trips, and Falls are common workplace accidents and biogas and RNG plants are no exception. This article highlights risks unique to these plants and proactive measures to keep your anaerobic digester facility running safely. Read the full article.
Three Unexpected Risks of Hydrogen Sulfide at RNG Plants
Explore three common scenarios where H2S can pose a threat in well-ventilated spaces and at well-maintained digester sites. Read the full article.
Get Insights from the Bioprocess Experts Right to Your inbox
Sign up to the Discover Digesters Newsletter to access Azura’s best practices, field-tested advice, and insights into the anaerobic digestion & industrial wastewater treatment industries.
By submitting this form, you are consenting to receive marketing emails from: Azura Associates. You can revoke your consent to receive emails at any time by using the SafeUnsubscribe® link, found at the bottom of every email. Emails are serviced by Constant Contact.