Foam is a messy, sticky, and smelly problem in biodigesters. But why does foam form in an anaerobic digester in the first place?
Foam develops from a combination of three conditions:
- Gas bubbles from the digestate – Biogas bubbles are present in normal conditions
- Surfactants strengthen the gas bubbles – Surfactants prevent the bubbles from bursting
- An operational event disrupts normal conditions – The event upsets the balance between bubble formation and bubble popping
Surfactants form the “skin” of a bubble. They can be chemical additives or produced in nature as biosurfactants. Surfactants often create and stabilize foam. Some surfactants that may be present in feedstocks are:
- Soap is a chemical surfactant
- Fats, oils, and greases (commonly called “FOG”) are common sources of biosurfactants
- Egg whites contain long protein molecules, while oil or FOG contains fat molecules, both of which can act as biosurfactants in large quantities within the digester
Bubbling in a digester is not a concern when gas production is at a controlled rate. The key word is controlled. The bubble formation rate is balanced with the popping rate during normal operations. When this balance is upset, bubbles do not “pop” as fast as they are formed, and this build-up of un-popped bubbles causes foaming. The video below shows a digester with a nicely balanced biogas bubble formation and popping rate.
But when gas production spikes or more surfactants accumulate, the foam may overflow and create a mess. The foam can flow from the digester into gas piping, pressure relief valves, flame arrestors, and even lift off a floating roof or tear a fabric gas dome! This kind of damage to the biogas collection, storage, and handling systems can create an uncontrolled release of biogas and is potentially a very serious safety and fire or explosion hazard. Foam can also be a biohazard that could cause slips, trips, and falls when released. Despite its impact on operations, foam is one of the most common preventable biodigester issues.
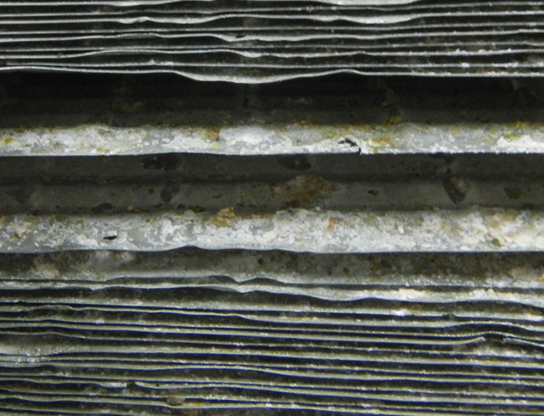
Severe anaerobic digester upsets may last 4-8 weeks and result in anywhere from 25% to 100% loss of both feedstock tipping or gate fee and RNG or biomethane gas revenue during that time. In Azura’s experience, most anaerobic digesters experience foaming at least once during their operational lifetime. Preventative measures reduce foam downtime more effectively than reactive measures. We wrote this article to help owners and operators better understand the science behind foam.
What Does the Foam in Your Digester Look Like?
Identifying the type of foam is a good start for a root cause analysis. Foam has two key traits: stability and bubble size. Stability is how long the bubbles last before popping. Some foams are so stable that they don’t break down easily, even with mixing. Mixing can even make more foam, by disturbing the bubbles in the digestate. It’s like shaking a can of beer – once you open it, you know foam will overflow!
Bubble size varies, ranging from large to tiny. Smaller bubbles can resemble milk foam on a cappuccino. The milk bubbles sit on the surface unless actively folded into the coffee. Foams with small bubbles tend to be more stable and harder to break down. The operational upsets that typically create small bubble foam also stabilizes foam. For example, receiving a shock load of high protein or high-fat feedstocks can increase the risk of creating a lot of biosurfactants in the biodigester. Long protein and fat molecules often biodegrade and break down to form biosurfactants. These biosurfactants then prevent the bubbles from bursting, thereby stabilizing the foam.
Small bubble foam tends to be a lot riskier for digester operations. This foam can be quite strong and even physically lift the roof off your digester or tear a biogas collection membrane. Due to its stability, resolving small bubble foam upsets generally takes longer. In the image below, Azura took a digestate sample from a foaming digester with smaller bubbles.
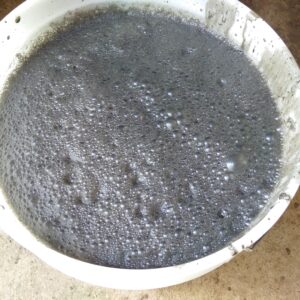
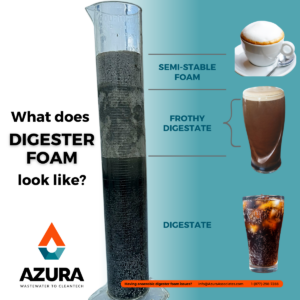
Larger bubbles can grow to the size of a beach ball! Big bubbles usually burst more easily but occupy more space. More foam means that the operators usually need to reduce feedstock dosing to the digester. This type of foam is more likely to rise into the tank headspace and enter the biogas collection piping and upgrading system as very large bubbles or tiny droplets, presenting significant health and safety risks. Larger bubble foams typically form more quickly than smaller bubble foams. For example, a facility may receive an acidic feedstock like fatty wastes one day. The next day, they receive an alkaline feedstock like bread and bakery waste. These wastes can mix in the receiving tank or in the digester, where it suddenly forms gas. Mixing acidic and alkaline feedstocks reacts similarly to vinegar and baking soda. The bubbles are formed very fast and may even lift the roof off the tank!
What Causes Foaming in Digesters?
It is crucial to understand what triggers foaming in anaerobic digesters. Foam in digesters results from a combination of gas production, surfactant accumulation, and operational events that tip the balance between bubble formation and bubble breakdown.
A sharp increase in gas production and surfactant accumulation can occur due to:
- Overfeeding (too much, too often, or inconsistently loading)
- Feeding imbalances (too much fat or protein in relation to the other feeds)
- Nutrient deficiencies (macronutrients, minerals, and micronutrients need to be in balance)
- Microbial shock (due to abrupt changes to temperature, pH, or exposure to inhibitory or toxic chemicals in the feed)
- Excess surfactants (can be produced from partially broken-down fats and protein, or from contaminants like cleaning agents and filamentous bacteria already in the feedstock)
Foaming often occurs when microbes struggle to break down waste efficiently. Overfeeding, nutrient deficiencies, and microbial shocks can slow them down.
Some conditions in sewage treatment systems and manure holding pits also encourage the growth of filamentous bacteria. These hair-like organisms can facilitate foam formation, mimicking the bubbling effects of using a loofah with soap.
There are over 16 types of filamentous bacteria that can grow in biodigesters. While microscopy or genetic testing can identify them, testing can be slow, costly, and often impractical. Results from genetic testing can take several weeks, meaning the foaming culprit may not be identified until it has passed completely through the system. Azura prioritizes quicker testing to make faster decisions during a foaming event. The most cost-effective approach is giving all the tools and knowledge to operators ahead of time. Empowered operators can mitigate damage to plant equipment and gas production.
Many operational events could cause gas production spikes and surfactant accumulation. Here are some common mistakes that can trigger foam:
- Overloading high protein feedstocks – example: too much slaughterhouse waste
- Excess ammonia-rich feedstocks – example: large loads of chicken manure
- Too much high-fat material – example: grease trap waste
- Rapid digestion of easily degraded feedstocks – example: feeding spoiled fruit juice too fast
- Overfeeding after an upset or shutdown – before microbes can fully recover from the upset
- Poor or inconsistent mixing – leading to uneven heating and digestion in the tank
- Nutrient imbalances – from a lack of variety or insufficiently nutritious feedstocks
- Undetected feedstock changes, for example:
- Large volumes of cleaning solution get mixed into slaughterhouse waste
- Higher fat levels in the DAF due to more effective coagulation
- Switching from iron chloride to aluminum-based or other coagulants, or switching the polymer flocculants used in the customer’s dissolved air flotation (DAF) treatment system, either change can introduce toxic or inhibitory compounds
Finding the root cause of foam can be difficult because there are so many potential causes. In Azura’s experience, overfeeding is the most common cause of foam. Most items on the list are related to organic loading and nutritional balance, which Azura will be diving deeper into in future content. Just like you were told growing up: you can’t live on soda and ice cream forever. Once in a while, you need to eat a broccoli! If you have any questions about overfeeding, email us at learn@AzuraAssociates.com.
What can I do when my digester is foaming?
Immediate Actions (within the first 24 hours)
If you are reading this article because your digester is currently foaming, then the first thing you need to do is reduce or stop feeding altogether. Next, try diluting the foam. If the foam is in the receiving pit, consider pumping a little into the digester so the bugs can work on eating the surfactants. If the feedstock tank overflows, nothing to do but clean it up! In the feedstock pit or a digester tank, you can try to break up the foam through mixing or spraying—try mixing for a short time and check on the results. Mixing can make foam problems better, or worse!
Be wary of any products that promise an all-encompassing cure to foam. Foam is one of the most common challenges in anaerobic digestion, especially when digesting multiple feedstocks and uncontrolled waste materials. Anti-foam products typically work by targeting a specific root cause. But since foam has several potential causes, no single anti-foam product will work for every case. Luckily, there are ways to manage foam without relying on these products.
Taking samples of the foam itself, digestate, and the feed tanks can help with a root cause analysis down the road.
Medium Term Actions (within the next few days or weeks)
The top two priorities in the next few days are:
- Slowly increase the temperature of the biodigester – Increasing the temperature of the biodigester by 0.5°C/1°F everyday can speed up the break down of the waste. Only increase the temperature if the ammonia levels and temperature are not concerning to start with.
- Slowly return to normal pH, volatile fatty acid (VFA), and total alkalinity (ALK) levels – Return to the levels that are normal to your specific operations. Having stopped feeding already, your digester should start returning to normal levels as your biomass eats through the accumulated material in the digester.
You can help balance your digester’s pH by leveraging your feedstocks’ natural properties. If the digestate is too acidic, pause acidic feeds and gradually add more alkaline feedstocks, or even think about alkaline chemicals like baking soda, caustic soda, or potassium hydroxide depending on your situation. If it’s too alkaline, reduce alkaline feedstocks and introduce more acid feedstock or feedstocks high in sugar with low alkalinity. Just like alkaline feeds, you may think about mildly acidic materials depending on your situation. Always adjust slowly to avoid microbial shocks and gas spikes. Dilution with well water, rainwater, or dilute feedstocks can also dilute problematic chemistry issues while you stabilize the pH.
Other tasks:
Returning to a nutrient balance will help the microbial population grow. A larger population can eat more of the waste. All the macronutrients, mineral, and micronutrients should be in balance. A good starting point would be to determine the current carbon/nitrogen/phosphorus (C/N/P) ratio, then rebalancing them as needed. For mineral components check sodium, potassium, calcium, magnesium, and iron.
There are many micronutrients (sometimes called “trace metals”), but the top three to check are nickel, cobalt, and molybdenum. Trace metal deficiency is a common cause of foaming but be wary about buying magic nonsense off the internet. Some solutions are scientifically backed, and some are pure pixie dust.
Sign up for the Azura newsletter and you’ll get future issues where we dig into all the details of macronutrients, minerals, and micronutrient balancing. We’ll be outlining digester testing and how to source low-cost supplements from your local animal feed mill, if needed. Don’t worry though, after more than 30 years of working with anaerobic digesters, we find that more than 75% of digesters are NOT helped by adding trace metals.
Long Term Actions (for the next few weeks)
Once the foam has mostly cleared, the next step is to identify the root cause and put preventative measures in place.
For a foam root cause analysis, Azura usually starts by reviewing changes in:
- Gas production, both volumes and composition,
- Feeding history and changes to the customer operations that can result in changing feedstock to your food waste digester site
- Operational practices such as mixing and temperature history, equipment operation and tank clean out history, and
- Disinfectant or cleaning solutions used in farming practices or at customer sites.
Some of the common preventative measures that we recommend are:
- Feed high protein and fatty feedstocks slowly
- Track the Total Digestible Energy (TDE) of your feed blend to know how much of the different feedstocks you can safely add
- Track your nutrient balance, including minerals and trace metal additions
- Keep alkaline and acidic feedstocks in separate feed tanks
- Consider a thermal hydrolysis or acid-phase process to ‘pre-chew’ and blend the feedstocks ahead of the digester
Next, remember those samples you took during the panicked first day of the foam event? We may test samples of the feedstock, digestate, and the foam to better understand the root cause of your situation. Comparing samples from normal operations with those taken during foaming events also helps us identify the cause more accurately. Let us know at learn@AzuraAssociates.com if you think Azura should release a self-guided foam root cause analysis tool!
Conclusion
In summary, managing foam in anaerobic digesters requires quick action, thorough analysis, and a solid plan to prevent future issues. By understanding the root causes and implementing the right steps, you can better prevent foam and keep your system running smoothly. If you’re facing foam challenges or want to learn more about our Foam Response Plan or root cause analysis tool, don’t hesitate to reach out to the Azura team—we’re here to help!
Related Articles
Top 10 Things to Make Your Digester Biology Happy
Anaerobic digestion is a complex biological process that requires a great deal of nuance and subtlety to optimize its operation. This article looks at the 10 most critical aspects of AD and how to make them run for the best outcome. Read the full article.
Commonly Overlooked Reasons for Anaerobic Digester Failures
Based on more than 30 years experience with digester facilities, this article presents the top five commonly overlooked causes of digester failure so you can recognize and avoid these pitfalls. Read the full article.
Get Insights from the Bioprocess Experts Right to Your inbox
Sign up to the Discover Digesters Newsletter to access Azura’s best practices, field-tested advice, and insights into the anaerobic digestion & industrial wastewater treatment industries.
By submitting this form, you are consenting to receive marketing emails from: Azura Associates. You can revoke your consent to receive emails at any time by using the SafeUnsubscribe® link, found at the bottom of every email. Emails are serviced by Constant Contact.